Laserhärten - Grundlagen
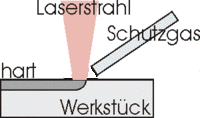
Beim Laserhärten wird ein Laserstrahl über das Werkstück geführt, sodass eine gehärtete Einzelspur entsteht. Das Material erwärmt sich dabei nur lokal im Laserbrennfleck, sodass es hier zur Austenitbildung kommt. Das benachbarte Material wird vom Laserstrahl nicht berührt und bleibt daher nahezu auf Raumtemperatur. Sobald sich das erhitzte Material nicht unter dem Laserstrahl befindet, fließt die Wärme sehr schnell in das umgebende Material ab und es bildet sich Martensit (Selbstabschreckung).
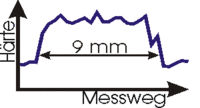
Die Selbstabschreckung ist viel schneller, als sie mit irgendeinem Kühlmedium erreicht werden kann. Durch diese Art der Abschreckung werden sowohl die hohen Härten als auch die Rissfreiheit erreicht. Da nur wenig Wärme eingebracht wird, bleibt der Verzug gering. Bei großen gehärteten Bauteilen kann es verzugsfrei bleiben.
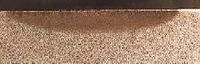
Eine beim Laserhärten entstehende Einzelspur im Querschliff ist nebenstehend gezeigt. Es bildet sich eine typische Härtelinse aus. Die Härteverläufe sind ebenfalls eingezeichnet. Die Härten fallen an den Spurgrenzen ziemlich scharf ab.
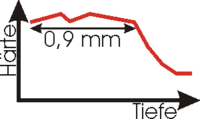
In dem gezeigten Beispiel ist die Spurbreite 9mm, die Einhärtetiefe 0,9mm. Gehärtet wurde von 280HV im Grundmaterial auf 800HV in der gehärteten Zone.
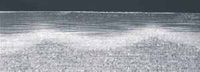
Durch Aneinanderlegen der lasergehärteten Einzelspuren können die einzelnen Spuren zu Flächen kombiniert werden. Im nebenstehenden Bild ist ein Querschliff durch eine solche Fläche gezeigt (51 CrV 4). Im Überlappbereich kann es allerdings zu einem Absinken der Härte kommen.
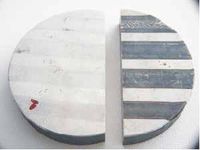
Durch Zufuhr von Schutzgas kann beim Laserhärten eine Oxidation der Oberfläche verhindert werden. Da die lokale Wärmeeinbringung auch die Verzugsfreiheit bzw. Verzugsarmut des Werkstücks garantiert, braucht in diesem Falle keine Nachbearbeitung zu erfolgen.
Im nebenstehenden Bild sind Härtespuren mit und ohne Schutzgas gezeigt
- rissfrei
- verzugsarm bis verzugsfrei
- oxidationsfreies Härten möglich
- Verkürzung der Prozesskette
- Vermeidung von Nacharbeit
- Zähigkeit des Grundwerkstoffes bleibt erhalten