Laser metal deposition
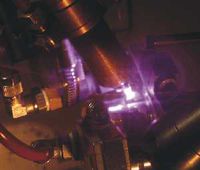
Material is applied for the purposes of repair or wear protection in laser metal deposition. The hardness and mechanical properties of the welded-on material can be precisely tailored to the load case.
Welded-on layers are conventionally applied with autogenous or electrical processes, which results in an extremely high thermal load and deformation. On the other hand, a precision laser is used in laser metal deposition or laser coating, so that welding beads with widths between 0 and 4mm can be welded on. This allows high precision deposit welding, and the low but concentrated heat input guarantees the minimum deformation possible.
As a result, laser metal deposition is eminently suitable for the repair of tools and machine components and wear protection.
Incidentally, the term hard facing is often also used to describe the wear protection of extremely hard parts. Furthermore, another word for laser metal deposition is lasering. It is particularly suitable for the laser coating of parts, which were previously chrome-plated for repair. The changeover from chromium plating to lasering is an important contribution to environmental protection, because toxic waste which has to be disposed of at great expense is not produced in laser surface treatment.
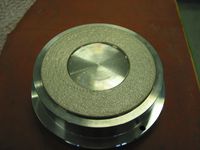
Advantages
The most important advantage of the laser metal deposition and laser coating is that very fine work can be performed owing to the precision laser. In this respect, the tracks are welded on with CNC control, so that the reproducibility is very high and larger volumes can also be quickly welded on. The welding process provides a long-lasting connection of base and filler material. At the same time, the heat input is so low, that there is hardly any deformation.
All types of metals can be processed with laser metal deposition. A wide range of usable filler materials is available in this respect. The welded-on layer can therefore be optimally tailored to the specific wear load. The hardness can be set between 20..65 HRC for most material variants in laser metal deposition. In addition to this, the laser metal deposition is optimally suited for melting hard materials (up to 2000 HV, wear protection). The optimization of the material for the repair of worn parts by laser metal deposition often provides a result which has far better properties than the original.
Particularly attractive benefits of laser surface treatment can be found in the business of repairing, because the change-over from chromium plating to lasering is both a gain for our environment and less expensive.